加工・材料の検討でローコスト設計のポイント
設備の加工サイズに合わせた寸法設計
設計時に機械仕様の考えのみで寸法を決め、加工設備を考えず、できた部品図をもとに加工設備を選択し加工業者様を探していました。それを自社/外注先の保有設備サイズに合わせた部品設計をすることで加工コストを抑えることができます。例)ガントリーローダーのビーム部分最大長さ8,900mmでは、加工機は10m以上のクラスが必要になります。このため加工機械が大型になればなるほど数が少なく、加工先が限定されるためコストアップの要因になっていました。
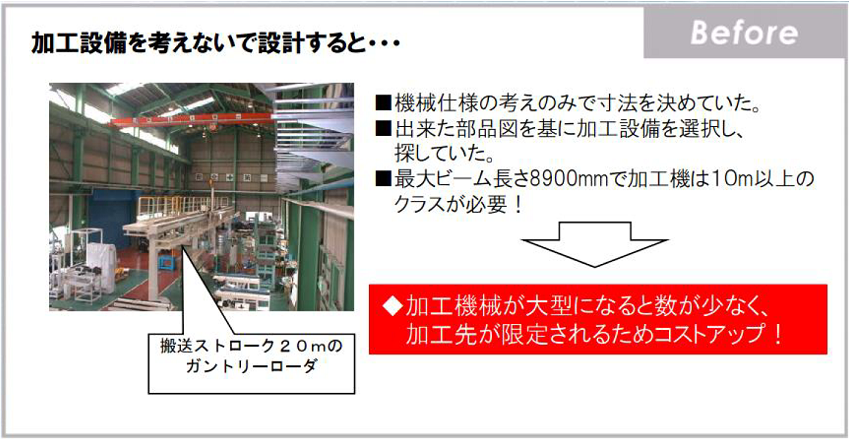
加工設備を考慮して分割可能部品は分割で設計する事で、加工先を限定しなくてもよくなりました。例えば、最大長さ6,700mmを支柱部で分割し6,000mm以下に設計し、加工業者様へ出せるようになりました。加工先の選択肢が広がり、加工時間の短縮またコストの低減にもつながります。注意点としましては、設計部門と生産管理部門とのコミュニケーションが大事なります。また部品によっては、強度や精度の影響があり、分割できない部品もあり検討が必要となります。
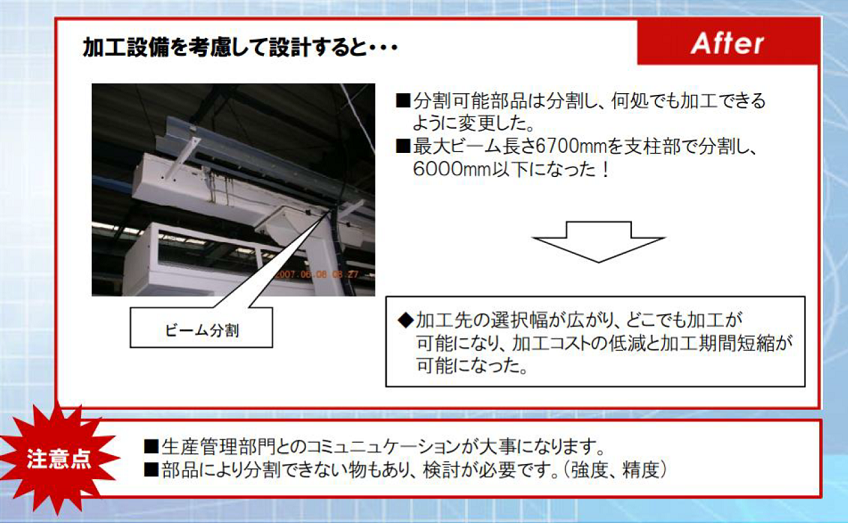
流通材料に合わせた寸法設計
機械設計にあたり設計者は規格ハンドブックのみでサイズを選定していたり、規格寸法は入手可能材料であると思い設計を進めていきますが、いざ部品加工に入る時材料の選定によって定尺材料の場合は、残材の買取りが必要になる事もあり、規格寸法だから大丈夫と考えても、流通していない材料だと入手困難でコストアップの要因になります。板厚、サイズなど市場に流通している材料を使用すること、流通材料に合わせた寸法設計をする事によりコストを下げることができます。

このことに考慮し設計することで、どこの業者様からでも入手可能になり、他に流用可能なため定尺材料でも残材の買取りが不要になりました。材料の入手がスムーズになり納期短縮にもつながりました。注意点としましては、社内での流通材料の情報共有またリスト化が必要になります。またミガキ材料は機械加工面の削減に有効となります。
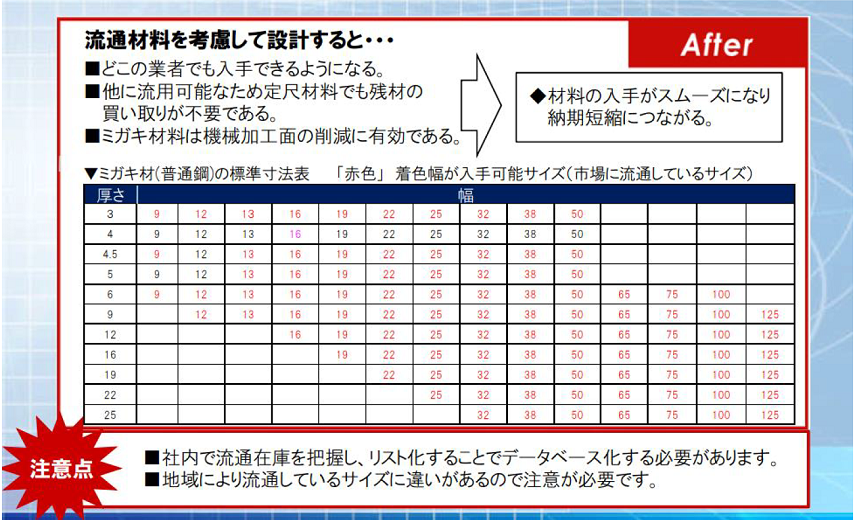
まとめ
エイ・テイ・シイ(株)では今後もローコスト設計のポイントを紹介させて頂きたいと思います。
少しでも皆様のお役に立てれば幸いです。今後ともどうぞよろしくお願い申し上げます。