ものづくりのフロントローディングとは
フロントローディングの意味
「フロントローディング」という言葉をどこかで耳にしたり目にする機会も多いと思いますが、すごく簡単に言うと「設計段階で人や時間をかけてよく確認してから製造段階へ進めていきましょう!そうすれば品質が安定して無駄なコストが省けますよ!」という話しです。
例えば、設計段階で3DCADを使用しある程度の形になったところで製造部門と組立時に発生する問題点や不具合を洗い出し、設計段階で修正をかけていくようなイメージです。
フロントローディングは、実際に製造してから試作によるテストを実施する工数を削減でき、事前に設計を最適化することで手戻りを極力防げるため、開発スピードの向上とコスト削減が見込めます。
ものづくりにおいて一般的には製品品質と製品コストの8割は設計で決まると言われています。製造工程が完成に近づけば近づくほど設計変更がしづらくなり、設計変更した場合のコストも大きくなります。
フロントローディングによる効果
図132-1は、仕様変更の自由度と品質・コストの確定度を示したものである。開発が進むに従って製造設備などが確定していくため、仕様変更の自由度は低下し、設計が完了した後の仕様変更の余地は極めて限定的なものとなる。その結果、仕様変更の自由度が高い設計段階で、製品の品質とコストの8割程度が決まることになるのである注4。
参照元:第1部第1章第3節 製造業の企業変革力を強化するデジタルトランスフォーメーション(DX)の推進
注4 日野三十四『実践 エンジニアリング・チェーン・マネジメント:IoTで設計開発革新』(2017年、日刊工業新聞社)
このため、できるだけ開発の初期段階であるエンジニアリングチェーンに資源を集中的に投入すること(「フロントローディング」注5)により、問題点の早期発見、品質向上、後工程での手戻りによるムダを少なくすることが決定的に重要になる(図132-2)。
注5 設計初期の段階に負荷を掛け、作業を前倒しで進めること。
フロントローディングの難しさ
確かにフロントローディングの意味もわかるし、これが確立できれば効果もあるんだろうな~と思いますがこれを実際に行うのが難しい!!人材が豊富な大手企業ならまだしも、特に弊社は特殊仕様の装置の設計製作を行っているためその都度設計が必要で限られたリソースをどこに投入するかその判断も難しいものとなります。
また、設計の前倒しといってそう簡単にできるものではありません。一般的に設計には出図(手配リストの発行)の期限が決められており、そこに間に合わすように作業を進める場合がほとんどだと思います。設計者から言わせるとフロントローディングで行うと通常よりも工数がかかるので出図までの期間を延ばしてほしいということがよくあります。
例えば分かりやすいように設計と製造と2つに分けて製品完成までの工数を10としてみましょう。フロントローディング導入前では設計が4に対して製造が6だったとします。フロントローディングを行った場合はどうでしょうか。確かに工数の割合が逆転していますが全体の工数は10のままです。設計段階でリソースを投入し問題点の早期発見や製造途中の手戻りが無くなったことで製造工数は大きく減っています。しかしこれでは設計者の言う通り設計業務量が増えたことによって今まで以上に出図までの時間を必要とするために設計としての期間が長くなる懸念があります。また昨今のように部品の長納期化など不透明な状況ではいち早く手配をすることが先決ですがこれではかえってデメリットです。

フロントローディングのポイント ~「じならし」と「トライ&エラーの繰り返し」~
問題はフロントローディングの名のもとに製品完成までの全体の工数が減ることなく設計へ業務が集中することです。本来のフロントローディングでは設計段階へリソースを投入し、いかに効率よく設計を終えるかということがポイントです。
冒頭の図をもう一度見てみましょう。設計段階へ負荷が移行しているのがよく分かりますがフロントローディングによって全体の負荷も下がっているのがわかります。(負荷の山が低くなり、負荷の面積も減少している)
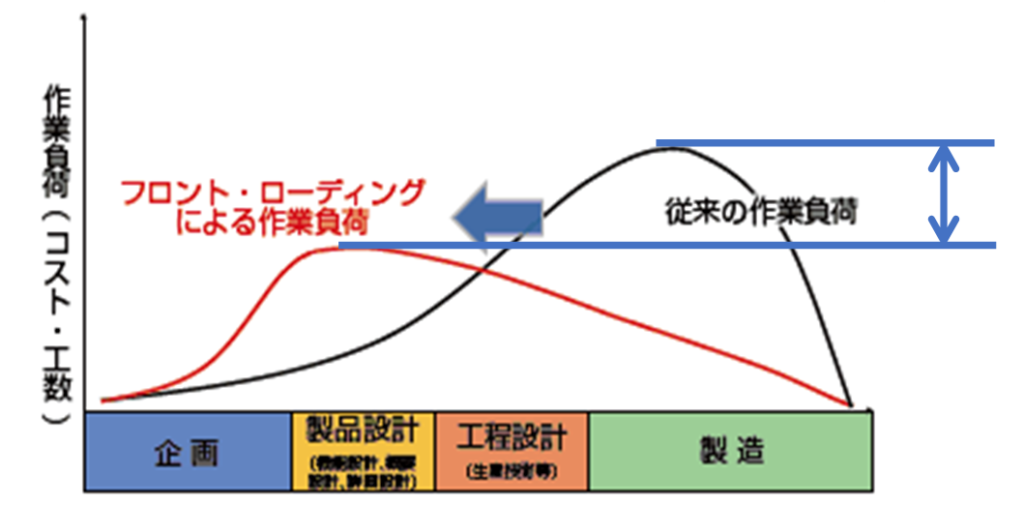
フロントローディング化も自動化導入に通ずるものがあると感じており、「じならし」 をしっかり行ってから導入を進めていく必要があります。今流行りのDX(デジタルトランスフォーメーション)も同じで単にデジタル化すればいいというわけではなくそこに効率化が見込めないと効果が薄れてしまいます。
また、多くの中小企業ではなかなかフロントローディング化やDX、自動化導入に専門で従事させることは難しく、通常業務と兼務になるパターンが多いかと思います。そいった意味でも「地ならし」をしっかり行って、まずは少しずつ取り組みを開始しトライ&エラーを繰り返し行うことで成果がでるのではないでしょうか。